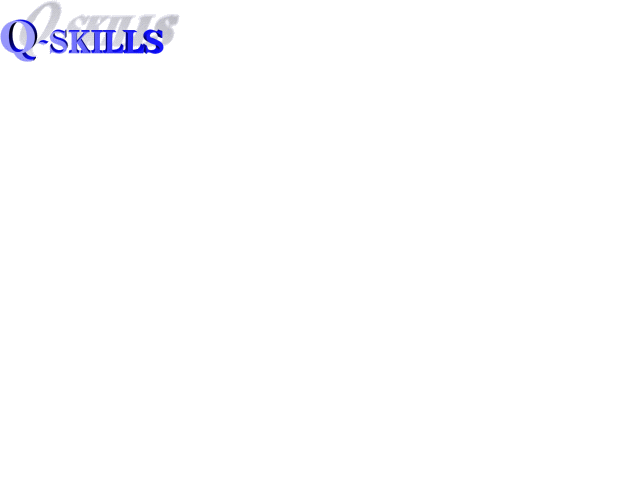
Multimedia Quality Tools
Training on your PC or Intranet
Quality Glossary
Advisor - See Facilitator/Advisor
Affinity Diagram - A way to organize idea data into coherent patterns or themes.
A large number of ideas are generated and then organized into groupings to reveal major themes.
Arrow Diagram - Related to PERT charts. Arrows are used to join a network of activities in sequence.
Attribute - Attribute data is data that is counted on the basis of whether or not it has a certain attribute or characteristic. eg number of errors per form. Attribute data is monitored using check sheets and attribute control charts.
Authoritarian Culture - An organizational culture characterized by the holding of all power (decision making and information) at the top of the organization. The authoritarian organization seeks to maintain the status quo and forces workers to conform, never question or give feedback, play politics, and wait for orders.
Bar Chart/Graph - A graph where the variable data is shown as the heights of vertical
(or horizontal) bars.
Benefit - See Outcome
Benchmarking - A continuous process of measurement of our products, services and work processes, against the toughest competitors, or those recognised as industry leaders. A fundamental outcome is to gain an understanding of our strengths and weaknesses.
Best Practice - The methods used in work processes, whose outputs best meet customer needs. Best practice may be revealed by benchmarking.
Boundary - The beginning or end point in the portion of a process from a Supplier to a Customer that will be the focus of the process improvement effort.
Brainstorming - A group decision-making technique designed to generate a large number of creative ideas through an interactive process. Brainstorming is used to generate alternative ideas to be considered in making decisions.
Capability, Process Capability - The capability of a process to produce defect free product. A process is 100% capable if it is "in control" and within Specification Limits.
Cause and Effect Diagram - See Ishikawa Diagram.
CBT - Computer Based Training such as Q-Skills. (Also CAL - Computer Aided Learning, CAT - Computer Aided Training)
Center Line - The line on a control chart that represents the average (mean or median) value of the items being plotted.
Check Sheet - A data collection form consisting of multiple categories. Each category has an operational definition and can be checked off as it occurs. Properly designed, the Check Sheet helps to summarize the data, which is often displayed in a Pareto Chart.
Coach - A key resource person from within the organization who will support the CEO's leadership of the CQI. A respected peer from the hospital work force who is enthusiastic and knowledgeable about CQI, eager to learn and eager to help others learn.
Collaborative Culture - An organizational culture characterized by a shared vision, shared leadership, empowered workers, cooperation among organizational units as they work to improve processes, a high degree of openness to feedback and data, and optimization of the organizational whole versus its many parts.
Common Cause System of Variation - The collection of variables that produce common cause variation and the interaction of those variables. Common causes are the result of random variations alone.
Continuous Quality Improvement (CQI) - The culture, strategies and methods necessary for continual improvement in meeting and exceeding customers' expectations.
Control Chart - A display of data in the order that they occur with statistically determined upper and lower limits of expected common cause variation. It is used to indicate special causes of process variation, to monitor a process for maintenance, and to determine if process changes have had the desired effect. One of the basic tools of the New Quality Technology.
Control limits - Expected limits of common cause variation. Sometimes they are referred to as upper and lower control limits. They are not specification or tolerance limits. They show "the voice of the process".
Customer - The receiver of an output of a process, either internal or external to an organization or corporate unit. A customer could be a person, a department, a company, etc.
Customer Data Table - A tool for translating customers' words into requirements, quality indicators and features of the product or service.
Data Collection - Gathering facts on how a process works and/or how a process is working from the customer's point of view. All data collection is driven by knowledge of the process and guided by statistical principles.
Deployment Chart - A form of modified flow chart. A flow chart has the name of each person responsible for each step added together with the duration of each step.
Deming Cycle for Continuous Improvement - A visualization of the CQI process usually consisting of four points - Plan, Do, Check, Act -- linked by quarter circles. The cycle was first developed by Dr. Walter A. Shewhart but was popularized in Japan in the 1950 by Dr. W. Edwards Deming.
Deming's 14 Points - The foundation of Deming's philosophy. The points are a blend of leadership, management theory, and statistical concepts which highlight the responsibilities of management while enhancing the capacities of employees.
Deming's fourteen points
1. Create constancy of purpose toward improvement of product and service with a plan to become competitive -- to stay in business and to provide jobs.
2. Adopt a new philosophy. We are in a new economic age. We can no longer live with commonly accepted levels of delays, mistakes, defective materials and defective workmanship.
3. Cease dependence on mass inspection. Require instead, statistical evidence that quality is built in to eliminate need for inspection on a mass basis.
4. End the practice of awarding business on the basis of price tag alone. Instead, depend on meaningful measures of quality along with price.
5. Improve constantly and forever the system of production and service. It is management s job to work continually on the system.
6. Institute a vigorous program of education and retraining.
7. Adopt and institute leadership. The responsibility of supervision must be changed from sheer numbers to quality. Improvement of quality will automatically improve productivity.
8. Drive out fear so that everyone may work effectively for the company.
9. Break down barriers between departments. People in research, design, sales and production must work as a team to foresee problems of production that may be encountered with various materials and specifications.
10. Eliminate numerical goals, posters and slogans for the workforce that ask for new levels of productivity without providing new methods.
11. Eliminate work standards that prescribe numerical quotas.
12. Remove barriers that stand between the hourly worker and his right to pride of workmanship.
13. Encourage education and self improvement for everyone.
14. Create a structure in top management that will push every day on the above thirteen points.
Deming's 5 principles:
1. The central problem in lack of quality is the failure of management to understand variation. (Everything varies. Statistics help us to predict how much it is going to vary.)
2. It is management s responsibility to know whether the problems are in the system or in the behavior of the people.
3. Teamwork should be based on knowledge, design, redesign and redesign. Constant improvement is management s responsibility. Most causes of low quality and productivity belong to the system.
4. Train people until they are in statistical control (until they are achieving as much as they can within the limits of the system you are using).
5. It is management s responsibility to give detailed specifications.
Distribution - The manner in which measurements for a process are spread out. A distribution may be shown using a histogram.
Facilitator/Advisor - A person who has developed special expertise in the CQI process. In a CQI team, the facilitator/advisor is not a team member but a person outside the group who serves as a process guide, teacher of CQI methods, and consultant to the team leader, and who helps connect the work of the team to the organization's overall CQI effort..
Fishbone Chart - See Cause and Effect Chart.
Flowchart - A graphical representation of the flow of a process. A useful way to examine how various steps in a process relate to each other, to define the boundaries of the process, to identify customer/supplier relationships in a process, to verify or
form the appropriate team, to create common understanding of the process flow, to determine the current "best method" of performing the process, and to identify redundancy, unnecessary complexity and inefficiency in a process.
FOCUS-PDCA - A strategy that provides a roadmap for continuous process improvement when linked to a quality definition. It is an acronym meaning: Find a process to improve, Organize a team that knows the process, Clarify current knowledge of the process, Understand sources of process variation, Select the process improvement, Plan the improvement and continued data collection, Do the improvement, data collection, and analysis, Check and study the results, Act to hold the gain and to continue to improve the process.
Force Field Analysis - A systematic method of understanding competing forces that increase or decrease the likelihood of successfully implementing change.
Future State - In an organizational transformation, the vision of where the organization will be after it is transformed. For the transformation to CQI, the future state includes constancy of purpose, leaders who model the new way, collaboration, customer mindedness, and a process focus.
Histogram - A bar graph showing the frequency of occurrence of a measured characteristic of a process. The measured value is divided into ranges or classes and the frequency in each range plotted.
Imagineering - A process wherein an ideal state is visualised and compared with the current one.
Immediate customer - The person or unit that directly receives the output of the process.
Input - The service or product a supplier provides to a process. Inputs to one process are the outputs from preceding processes.
Interrelationship Digraph - A way to display cause-and-effect relationships among all the elements in a system. The relationship arrows indicate the issues/causes that are the most fundamental among all the related items.
Ishikawa Diagram - A graphic tool used to explore and display all the factors that may influence or cause a given outcome. (Also known as a cause and effect or fishbone diagram.)
ISO - The set of International Standards relating to quality, including: ISO9000, ISO9001, ISO9002, ISO9004, ISO9004.4, QS9000
Key Process Variable - A component of the process that has a cause and effect relationship of sufficient magnitude with the Key Quality Characteristic such that manipulation and control of the KPV will reduce variation of the KQC and/or change its level.
Key Quality Characteristic - The most important quality characteristics. The KQCs must be operationally defined by combining knowledge of the customer with knowledge of the process. KQCs are measured to understand the actual performance of the process.
Mean - Average
Median - In a series of numbers, the median is a number which has at least half the values greater than or equal to it and at least half of them less than or equal to it.
Meeting Process - A defined method for conducting meetings that includes specific roles and responsibilities for a team leader, a recorder, a timekeeper, team members, and a facilitator or advisor. The steps are:
1) Clarify the objective,
2) Review roles,
3) Review the agenda,
4) Work through agenda items,
5) Review the meeting record,
6) Plan next steps and next meeting agenda and
7) Evaluate.
Mentor - A highly skilled CQI professional with extensive training and experience in the initiation and operation of CQI. A resource person from outside the organization or department who visits periodically to counsel the CEO, Coach and Quality Improvement Council in the development, implementation and evaluation of CQI.
Multiple Voting - A group decision-making technique designed to reduce a long list to a few ideas.
Nominal Group Brainstorming - A group process technique designed to efficiently
generate a large number of ideas through input from individual group members.
Normal distribution - A theoretical distribution, where deviations from the mean in either direction are equally likely and are due to chance. Means of large enough groups of samples from any distribution will be normally distributed (central-limit theorem). A normal distribution is symmetric and bell shaped, as shown below. Move the cursor over the graph, or type a value, to see how the percentage of defects changes with sigma, the standard deviation for the population
Operational Definition - A description in quantifiable terms of what to measure
and the steps to follow to measure it consistently. Deming has suggested that
a good operational definition includes:
1) a criterion to be applied,
2) a way to determine whether the criterion is satisfied, and
3) a way to interpret the results of the test. An operational definition is developed for each KQC or process variable before data is collected.
Opportunity Statement - A concise description of a process in need of improvement, its boundaries, and the general area of concern where a CQI Team should begin its efforts.
Outcome (Benefit) - The degree to which Outputs meet the needs and expectations of the Customer.
Output - The service or product that a customer receives from a process. The output of one process can be the input to a succeeding process.
Owner - The person who has or is given the responsibility and authority to lead the continuing improvement of a process. Process ownership is a designation made by leaders of organizations and depends on the boundaries of the process.
Paradigm Shift - A point in time when the knowledge or structure which underlies a science or discipline changes in such a fundamental way that the beliefs and behavior of the people involved in the science or discipline are changed.
Pareto Chart - A bar graph used to arrange information in such a way that priorities for process improvement can be established. It displays the relative importance of data and is used to direct efforts to the biggest improvement opportunity by highlighting the vital few in contrast to the many others.
Penny Matrix - A way to prioritize a list of options by pooling the opinions of raters. Raters "spend" their pennies across several options with the sums of "money spent" indicating a priority weighting and ranking to the options.
Pert Chart - It is used to help plan and schedule actions, people and times in a project.
It usually shows a "critical path". This is a sequence of actions upon which the overall timing of the project depends.
Pie chart - A graph that looks like a pie. Pie charts are used to make it easy to visualise the relative proportions or magnitudes of variables in a period.
Population - A theoretical, infinitely large sample.
Present State - In a force field analysis, the description of an organization as it currently exists. It includes what happens in the organization, both formally and informally.
Prioritization Matrix - A way to prioritize options by requiring the raters to work to consensus on priorities. Also known as a paired-comparison technique., the tool pairs each option with each other, with row totals indicating weighting and ranking.
Process - A series of actions which repeatedly come together to transform Inputs provided by a Supplier into Outputs received by a Customer. A process can be used to develop products and services.
Process Decision Program Chart (PDPC) - A tool for improving implementation through contingency planning. By considering "what could go wrong?", plans for prevention of problems are generated.
Process Improvement - The continuous endeavor to learn about all aspects of a process and to use this knowledge to change the process to reduce variation and complexity and to improve customer judgments of quality. CFI begins by understanding how customers judge quality, how processes work, and how understanding the variation in those processes can lead to wise management action.
Process Owner - See Owner.
Process Variation - The spread of process output over time. There is variation in every process, and all variation is caused. The causes are of two types - special or common. A process can have both types of variation at the same time or only common cause variation. The management action necessary to improve the process is very different in each situation.
Quality Characteristics - Characteristics of the output of a process that are important to the customer. The identification of quality characteristics requires knowledge of the customer needs and expectations.
Quality Improvement Council (QIC) - A group composed of the Coach and the senior leadership of an organization which is primarily responsible for planning, strategy development, deployment, monitoring, educating, and promoting CQI.
Quality Inspection - Usually consists of three stages - sampling, measuring, and sorting. While many organizations rely on inspection to improve quality, the better way is to design quality into the product or service - to improve the process. This may include some inspection as a means of data gathering.
Quality Planning/Redesign - Creating new or redesigned products/services/processes to meet customer requirements. The steps of this method are Organize the project, Identify key customers, Determine requirements, Establish quality indicators, Design, Strengthen the design, Test the design, Implement and improve.
Red Bead Experiment - A simple exercise to demonstrate, among other things, that many managers hold workers to standards beyond their control, variation is part of any process, and workers work within a system beyond their control. The game also shows that some workers will always be above average, some average, and some below average, that the system, not the skills of individual workers, determines to a large extent how workers in repeating processes perform, and that only management can change the system or empower others to change it.
Refreezing - Recognizing, reinforcing, and rewarding new organizational attitudes and behaviors so they become the norm. Making processes, systems, and methods throughout the organization support CQI.
Relations diagram - A TQM tool used to analyse problems with complex interrelations.
Requirement-Indicator Matrix - A matrix that shows the presence of all possible relationships between customer requirements and quality indicators.
Rework - The act of doing something again because it was not done right the first time. It can occur for a variety of reasons, including insufficient planning, failure of a customer to specify the needed input, and failure of a supplier to provide a consistently high quality output.
Run - A point or a consecutive number of points that are above or below the central line in a run chart. Too long a run or too many or too few runs can be evidence of the existence of special causes of variation.
Run Chart - A display of data in the order that they occur. Run charts display process variation and can be used to indicate special causes of process variation in the form of trends, shifts, or other non-random patterns.
Seven-step Meeting Process - See Meeting Process.
Special Cause Variation - Variation in the process that is assignable to a specific cause or causes. It arises because of special circumstances.
Special and Common Cause System of Variation - The collection of variables that
produce both common cause variation and special cause variation and the interaction of those variables.
Spider Diagram - A visual report card for the performance of a number of indicators on a single chart. Also know as a "radar chart" and a "gap analysis" tool, this diagram makes visible the gaps between the current and desired performance.
Sponsor - A member of the organizational leadership who serves as an advocate or champion for a process improvement, assists in securing resources, and gives guidance to the effort.
Storytelling - A major accelerator of the process of organization wide CQI that uses Storybooks to follow steps in the QI or QP strategy. Storybooks and Storyboards help teams organize their work and their presentations so others can more readily learn from them. Use of Storyboards and Storybooks reduces variation in the process of Storytelling so the focus of learning is on content, not the method of telling. Storybooks form a permanent record of a team's actions and achievements and all the data generated, and Storyboards can function as the working minutes of a team.
Supplier - The party or entity responsible for an input to a process. A supplier could be a person, a department, a company, a nursing school, etc.
Taguchi Loss Function - The traditional view is that provided a product or service is within specification, everything is OK. The Taguchi Loss Function (proposed by Genichi Taguchi) says that the cost/benefits of any product or service can be described by a curve that has an optimum point. Any departure from this optimum is undesirable, despite being within specification. Total costs should be managed, and the process continually improved, even when within specification.
Tampering - Taking action without taking into account the difference between special and common cause variation.
Team Leader - A person designated to lead the CQI Team. An individual who has team leadership skills and basic quality improvement skills.
Teams
Cross-functional - A group of usually five to eight people from two or more areas of the organization who are addressing an issue which impacts the operations of each area. For example, the processes of meeting information requests might be addressed by a team involving PI,, managed care and marketing staff.
Functional - A group of five to eight people addressing an issue where any recommended changes would not be likely to affect people outside the specific area. For example, a Functional Team concerned with filing and retrieving data in the laboratory might consist just of people who work in the lab.
Transformation - A major organizational change from the present state to a new/preferred state in which CQI flourishes. The primary steps involved in moving an organization through a transformation are present state, unfreezing, transition period, refreezing, and new/preferred state.
Transition Period - A description of the time when an organization is visibly moving away from the old way toward the new way. During this time, employee attitudes and behaviors range from being excited and busy to being confused and resistant. The support for change is building. New leaders emerge, champions of the change come forward and confusion over roles begins to clear.
Tree Diagram - A tool to expand a proposed change from a general idea to a specific series of concepts or actions. Used to systematically map out in increasing detail the full range of paths and tasks that need to be accomplished to achieve a primary goal and related subgoals.
Ultimate Customer - The person or unit who receives the output from a series of processes and for who these processes are designed. Without the ultimate customer, there would be no need for the intermediate processes to exist.
Unfreezing - Reassessing old values and behaviors and becoming open to the acceptance of a new culture.
Meeting Process - A defined method for conducting meetings that includes
specific roles and responsibilities for a team leader, a recorder, a
timekeeper, team members, and a facilitator or advisor. The steps are
1)Clarify the objective,
2) Review roles,
3) Review the agenda,
4) Work throughagenda items,
5) Review the meeting record,
6) Plan next steps and next meeting agenda and
7) Evaluate.
Mentor - A highly skilled CQI professional with extensive training and
experience in the initiation and operation of CQI. A resource person from
outside the organization or department who visits periodically to counsel the
CEO, Coach and Quality Improvement Council in the development, implementation
and evaluation of CQI.
Multiple Voting - A group decision-making technique designed to reduce a long
list to a few ideas.
Nominal Group Brainstorming - A group process technique designed to
efficiently generate a large number of ideas through input from individual
group members.
Operational Definition - A description in quantifiable terms of what to
measure and the steps to follow to measure it consistently. Deming has
suggested that a good operational definition includes: 1) a criterion to be
applied, 2) a way to determine whether the criterion is satisfied, and 3) a
way to interpret the results of the test. An operational definition is
developed for each KQC or process variable before data is collected.
Opportunity Statement - A concise description of a process in need of
improvement, its boundaries, and the general area of concern where a CQI Team
should begin its efforts.
Outcome (Benefit) - The degree to which Outputs meet the needs and
expectations of the Customer.
Output - The service or product that a customer receives from a process. The
output of one process can be the input to a succeeding process.
Owner - The person who has or is given the responsibility and authority to
lead the continuing improvement of a process. Process ownership is a
designation made by leaders of organizations and depends on the boundaries of
the process.
Paradigm Shift - A point in time when the knowledge or structure which
underlies a science or discipline changes in such a fundamental way that the
beliefs and behavior of the people involved in the science or discipline are
changed.
Pareto Chart - A bar graph used to arrange information in such a way that
priorities for process improvement can be established. It displays the
relative importance of data and is used to direct efforts to the biggest
improvement opportunity by highlighting the vital few in contrast to the many
others.
Penny Matrix - A way to prioritize a list of options by pooling the opinions
of raters. Raters "spend" their pennies across several options with the sums
of "money spent" indicating a priority weighting and ranking to the options.
Present State - In a force field analysis, the description of an organization
as it currently exists. It includes what happens in the organization, both
formally and informally.
Prioritization Matrix - A way to prioritize options by requiring the raters
to work to consensus on priorities. Also known as a paired-comparison
technique., the tool pairs each option with each other, with row totals
indicating weighting and ranking.
Process - A series of actions which repeatedly come together to transform
Inputs provided by a Supplier into Outputs received by a Customer. A process
can be used to develop products and services.
Process Decision Program Chart (PDPC) - A tool for improving implementation
through contingency planning. By considering "what could go wrong?", plans
for prevention of problems are generated.
Process Improvement - The continuous endeavor to learn about all aspects of a
process and to use this knowledge to change the process to reduce variation
and complexity and to improve customer judgments of quality. CFI begins by
understanding how customers judge quality, how processes work, and how
understanding the variation in those processes can lead to wise management
action.
Process Mapping (BPM - business process mapping; BPR - business process re-engineering) - A flowchart showing process flows between departments or areas.
Process Owner - See Owner.
Process Variation - The spread of process output over time. There is
variation in every process, and all variation is caused. The causes are of
two types - special or common. A process can have both types of variation at
the same time or only common cause variation. The management action
necessary to improve the process is very different in each situation.
Quality - The many definitions of quality include:
"The sum of the characteristics that determines if a product is suitable for what it is intended" (Japanese standard)
"Fitness for use" (Juran)
"Conformance to requirements" (Crosby)
"The degree of excellence"
"Continually satisfying customer requirements"
"On target with minimum variance" (Wheeler)
Quality Characteristics - Characteristics of the output of a process that are
important to the customer. The identification of quality characteristics
requires knowledge of the customer needs and expectations.
Quality Improvement Council (QIC) - A group composed of the Coach and the
senior leadership of an organization which is primarily responsible for
planning, strategy development, deployment, monitoring, educating, and
promoting CQI.
Quality Inspection - Usually consists of three stages - sampling, measuring,
and sorting. While many organizations rely on inspection to improve quality,
the better way is to design quality into the product or service - to improve
the process. This may include some inspection as a means of data gathering.
Quality Planning/Redesign - Creating new or redesigned
products/services/processes to meet customer requirements. The steps of this
method are Organize the project, Identify key customers, Determine
requirements, Establish quality indicators, Design, Strengthen the design,
Test the design, Implement and improve.
Quality Tools - The set of tools including histograms, control charts, check sheets, Pareto charts, brainstorming, affinity diagrams, cause and effect diagram used in process improvement and process problem solving.
Red Bead Experiment - A simple exercise to demonstrate, among other things,
that many managers hold workers to standards beyond their control, variation
is part of any process, and workers work within a system beyond their
control. The game also shows that some workers will always be above average,
some average, and some below average, that the system, not the skills of
individual workers, determines to a large extent how workers in repeating
processes perform, and that only management can change the system or empower
others to change it.
Refreezing - Recognizing, reinforcing, and rewarding new organizational
attitudes and behaviors so they become the norm. Making processes, systems,
and methods throughout the organization support CQI.
Requirement-Indicator Matrix - A matrix that shows the presence of all
possible relationships between customer requirements and quality indicators.
Rework - The act of doing something again because it was not done right the
first time. It can occur for a variety of reasons, including insufficient
planning, failure of a customer to specify the needed input, and failure of a
supplier to provide a consistently high quality output.
Run - A point or a consecutive number of points that are above or below the
central line in a run chart. Too long a run or too many or too few runs can
be evidence of the existence of special causes of variation.
Run Chart - A display of data in the order that they occur. Run charts
display process variation and can be used to indicate special causes of
process variation in the form of trends, shifts, or other non-random
patterns.
Seven-step Meeting Process - See Meeting Process.
Scatter diagram - A graphical analysis of the relationship between two variables. It can be used to help screen for possible cause and effect relationships.
Six sigma ( 6 sigma) - An expression that literally means six standard deviations of a population. It refers to a distribution with a total spread of 12 sigma. (Most companies base operations on "3 sigma".) It effectively implies zero defects. Six sigma is the basis of a management philosophy which considers that any defect results in hidden downstream problems, costs and hence reduced customer satisfaction.
Skew distribution - A non symmetrical distribution.
SPC - Statistical Process Control - A methodology using control charts and other tools to improve processes.
Special Cause Variation - Variation in the process that is assignable to a
specific cause or causes, other than random variation. It arises because of special circumstances.
Special and Common Cause System of Variation - The collection of variables
that produce both common cause variation and special cause variation and the
interaction of those variables.
Spider Diagram - A visual report card for the performance of a number of
indicators on a single chart. Also know as a "radar chart" and a "gap
analysis" tool, this diagram makes visible the gaps between the current and
desired performance.
Sponsor - A member of the organizational leadership who serves as an advocate
or champion for a process improvement, assists in securing resources, and
gives guidance to the effort.
Standard deviation - The square root of the average squared difference between individual measurements and the mean of a sample.
Storytelling - A major accelerator of the process of organization wide CQI
that uses Storybooks to follow steps in the QI or QP strategy. Storybooks
and Storyboards help teams organize their work and their presentations so
others can more readily learn from them. Use of Storyboards and Storybooks
reduces variation in the process of Storytelling so the focus of learning is
on content, not the method of telling. Storybooks form a permanent record of
a team's actions and achievements and all the data generated, and Storyboards
can function as the working minutes of a team.
Stratification - A process of grouping data according to a common characteristic.
eg Data grouped by operator.
Supplier - The party or entity responsible for an input to a process. A
supplier could be a person, a department, a company, a nursing school, etc.
Systematic Diagram - A root and branch style TQM diagram. It is used to build structures through levels. There are two types:
Plan-development; used to develop methods and policies.
Component-development; used to structure the elements of an activity.
Tampering - Taking action without taking into account the difference between
special and common cause variation.
Team Leader - A person designated to lead the CQI Team. An individual who
has team leadership skills and basic quality improvement skills.
Teams
Cross-functional - A group of usually five to eight people from two or
more areas of the organization who are addressing an issue which impacts the
operations of each area. For example, the processes of meeting information
requests might be addressed by a team involving PI,, managed care and
marketing staff.
Functional - A group of five to eight people addressing an issue where
any recommended changes would not be likely to affect people outside the
specific area. For example, a Functional Team concerned with filing and
retrieving data in the laboratory might consist just of people who work in
the lab.
TQM - Total Quality Management
Transformation - A major organizational change from the present state to a
new/preferred state in which CQI flourishes. The primary steps involved in
moving an organization through a transformation are present state,
unfreezing, transition period, refreezing, and new/preferred state.
Transition Period - A description of the time when an organization is visibly
moving away from the old way toward the new way. During this time, employee
attitudes and behaviors range from being excited and busy to being confused
and resistant. The support for change is building. New leaders emerge,
champions of the change come forward and confusion over roles begins to
clear.
Tree Diagram - A tool to expand a proposed change from a general idea to a
specific series of concepts or actions. Used to systematically map out in
increasing detail the full range of paths and tasks that need to be
accomplished to achieve a primary goal and related subgoals.
Ultimate Customer - The person or unit who receives the output from a series
of processes and for who these processes are designed. Without the ultimate
customer, there would be no need for the intermediate processes to exist.
Unfreezing - Reassessing old values and behaviors and becoming open to the
acceptance of a new culture.
Q-Skills may be useful to you if
you have an interest in any of the following areas: qskills, intranet, PC based,
internet, TQM, total quality management, quality improvement, process
improvement, quality training, team support, team training, CAL, survey
software, computer aided learning, CBT, computer based training, CAT, quality
improvement training, computer aided training, tutorial, interactive multimedia,
BPR, re-engineering, BPM, flowcharter, business process mapping,
swimlane, costing, user defined variables, flow chart, easy to use, automatic
line drawing, validity checking, improvement tools, improvement techniques,
Pareto, brainstorming, histogram, cause and effect, flowcharter, C &
E, attribute control chart, graph, range, averages, control chart, check
sheet, affinity diagram, random sampling, statification, SPC, statistical
process control, facilitator support, normal distribution,
six sigma, 6 sigma, zero defects, software, toolkit, toolbox, FMEA,
analysis, automatic documentation generation, ISO 9000, ISO9001,
ISO9002, QS9000, ISO9004, ISO9004.4, MS, Microsoft Windows 3.0, Windows
3.1, Win 95, IE4, IE5, IE5.5, Win NT, quality improvement training, computer based training,
quality tools, flowcharter, BPM, brainstorm, control chart, survey software.